Cement is one of the most important materials for building our homes, roads, and cities. But did you know that making cement also produces a lot of carbon dioxide (CO₂), which harms our planet?
The cement industry contributes 7% – 8% of the total emissions of the world. During the production of cement, the factory releases up to 0.8 kg of carbon dioxide (CO2) to produce 1 kg of cement.
Factories of all industries burn fossil fuels and release CO₂ from raw materials, making it hard to keep the air clean. However, many smart solutions have been invented to reduce carbon footprints while keeping cement production efficient.
From using cleaner energy sources like solar and wind to switching to better raw materials, the cement industry is finding new ways to be eco-friendly. The government is also introducing policies and trading systems to control emissions.
Read on to discover how these changes are making a difference!
Cement Industry in India
Before understanding how to reduce carbon footprint, let’s learn about the cement industry in India. India ranks as the second-largest producer of cement globally, contributing over 8% to the worldwide installed capacity.
Cement production in FY23 reached 374.55 million tonnes, marking a 6.83% year-on-year growth. In FY24, production is projected to increase by 7-8%, driven by ongoing infrastructure and residential development projects.
The sector’s capacity is forecasted to grow at a CAGR of 4-5%, reaching 715-725 million tonnes per year by FY27, with consumption estimated at 450.78 million tonnes.
Leading companies such as UltraTech, ACC-Ambuja, Shree Cement, and Dalmia Cement are poised to expand their capacity in FY25. Around 70% of the country’s total cement production is generated by the top 20 companies.
Why is the Cement Industry a Major Contributor to Carbon Emissions?
The cement industry is a major contributor to carbon emissions because making cement requires a lot of heat and energy. Cement factories burn fuels like coal, oil, and gas, which release carbon dioxide (CO₂) for heat generation purposes. Also, when limestone is heated to make cement, it naturally releases CO₂. These two processes create a large amount of pollution. So, the question arises ‘How to reduce carbon footprint’?
To reduce carbon footprints, factories can use cleaner fuels, recycle heat, and mix cement with other materials like fly ash. Using renewable energy, such as solar or wind power, can also help reduce Scope 2 emissions of the process. Scientists are finding ways for carbon emission reduction by capturing CO₂ before it goes into the air. If factories use these new methods, they can still make cement while protecting the environment.
What are the Best Practices for Carbon Emission Reduction in the Cement Industry?
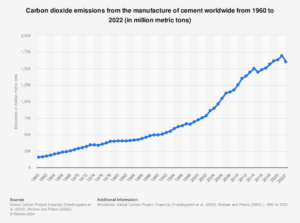
The cement industry is a significant source of carbon emissions, contributing about 8% of the world’s CO₂ emissions. To reduce carbon footprints several strategies are being explored. Implementing these strategies can also help the cement industry contribute to global efforts to reduce greenhouse gas emissions.
Clinker, the main ingredient in cement, is highly carbon-intensive, accounting for 90% of the cement industry’s emissions. Reducing its use can significantly lower emissions. One promising method is using Limestone Calcined Clay Cement (LC3), which replaces half of the clinker with calcined clay and limestone.
This approach can reduce CO₂ emissions by around 40% compared to traditional cement. Additionally, researchers are developing techniques to recycle materials from demolished buildings to produce cleaner clinker, potentially saving up to three gigatonnes of CO₂ annually.
Heating limestone releases a substantial amount of CO₂ during clinker production. Alternative processes aim to replace limestone with other materials. For example, some companies are developing methods to produce cement from carbon-free calcium silicate rocks, which are abundant and do not emit CO₂ when processed. This innovation could significantly reduce carbon footprints caused due to cement production.
Carbon capture, utilization, and storage (CCUS) is a key strategy for reducing emissions in the cement industry. This technology involves capturing CO₂ emissions from cement plants and storing them underground or utilizing them in other industrial processes. Projections indicate that CCUS could reduce carbon emissions by 36%, making it a vital tool for achieving net-zero goals in the sector.
- Fuel Switching and Electrification
Most cement factories burn coal and oil, which releases a lot of CO₂. Switching to cleaner fuels like hydrogen and electricity from renewable sources like solar energy can reduce carbon footprints and make production greener. Using electric-powered kilns instead of fossil fuels can further lower emissions. This shift improves air quality and supports reducing greenhouse gas emissions globally.
What are the Challenges in Reducing Carbon Emissions?
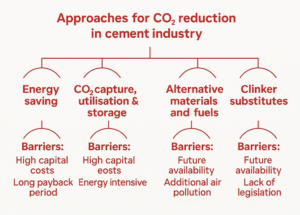
Carbon emissions reduction in the cement industry is challenging due to several factors. Addressing these challenges requires collaboration between scientists, industry leaders, and governments to develop affordable and effective solutions to reduce carbon footprints caused due to the cement industry.
Producing cement requires heating materials to very high temperatures, which consumes a lot of energy. This process often relies on burning fossil fuels, leading to significant carbon emissions.
The main ingredient in cement is limestone. When heated, limestone releases carbon dioxide (CO₂) as part of a chemical reaction. This means that even if cleaner energy is used, CO₂ is still emitted from the materials themselves.
Implementing new technologies to reduce emissions can be expensive. Many cement companies operate on thin profit margins, making it difficult to invest in eco-friendly equipment or processes.
Some proposed methods for reducing emissions are still in the research phase. They may not yet be practical or effective for large-scale use in cement production.
Environmental regulations vary by region. Inconsistent rules can make it hard for companies to adopt uniform strategies to reduce carbon footprints.
What are scope 1, scope 2 and scope 3 emissions for Cement Industry?
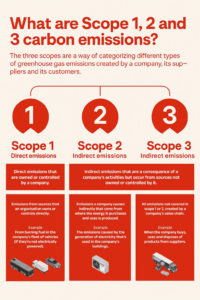
In the cement industry, understanding Scope 1, Scope 2, and Scope 3 emissions is essential to identify and manage sources of greenhouse gas emissions effectively. By addressing all three scopes, the cement industry can develop comprehensive strategies to reduce carbon footprints and mitigate its impact on climate change.
These are direct emissions from sources that the cement company owns or controls. In cement production, this includes CO₂ released during the chemical transformation of limestone into clinker, as well as emissions from burning fuels like coal in the kilns.
These are indirect emissions from the generation of purchased energy that the company uses. For cement manufacturers, this primarily involves the CO₂ emissions from the electricity consumed to operate machinery and other equipment.
These encompass all other indirect emissions that occur in the company’s value chain. For the cement industry, this includes emissions from activities such as extracting and transporting raw materials, employee travel, and the emissions produced when customers use the cement in construction.
Government Regulations and Policies
The Indian government has introduced new rules to reduce carbon footprints in industries like cement, aluminium, and textiles. These regulations encourage companies to lower emissions and adopt greener practices.
Carbon Credit Trading Scheme (CCTS)
- Introduced in July 2024 for reducing greenhouse gas emissions.
- Companies earn Carbon Credit Certificates (CCCs) for reducing emissions.
- Each CCC represents one ton of CO₂ reduced or removed.
Role of Government Agencies
- The Ministry of Power oversees the scheme.
- The Bureau of Energy Efficiency (BEE) manages its operations.
How does the System Work?
- Industries get specific emission reduction targets.
- Companies exceeding their limit must buy carbon credits, encouraging greener production.
These policies help India fight climate change and reduce carbon footprints in key industries.
What is Sunsure Energy's Role in Carbon Emission Reduction?
We at Sunsure Energy, are helping multiple companies across different industries to reduce carbon footprint by providing clean energy solutions. We develop renewable energy projects, like open access solar projects to supply green power to factories.
By switching from fossil fuels to Sunsure’s renewable energy, your cement factory can lower its CO₂ emissions and achieve significant carbon emission reduction. This not only helps the environment but also supports India’s goal of becoming more sustainable.
Conclusion
The cement industry is working hard to become greener by using cleaner energy, better technology, and smart government policies. With companies adopting renewable power and new ways to make cement, there is hope for a cleaner future. Programs like carbon credit trading also encourage factories to lower their emissions.
Everyone has a role to play in protecting the planet. By supporting industries that focus on sustainability, we can help reduce carbon footprints and slow down climate change. Small steps today can make a big difference for tomorrow!